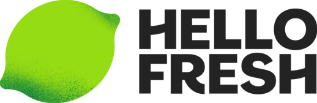
How HelloFresh Reduced Supplier Costs and Scaled Quality with Intelex
HelloFresh is the world’s leading meal kit provider, delivering fresh, pre-portioned ingredients and chef-curated recipes to millions of households. With a strong focus on sustainability, food safety, and quality, HelloFresh reduces food waste while ensuring the highest standards of food safety and customer experience.
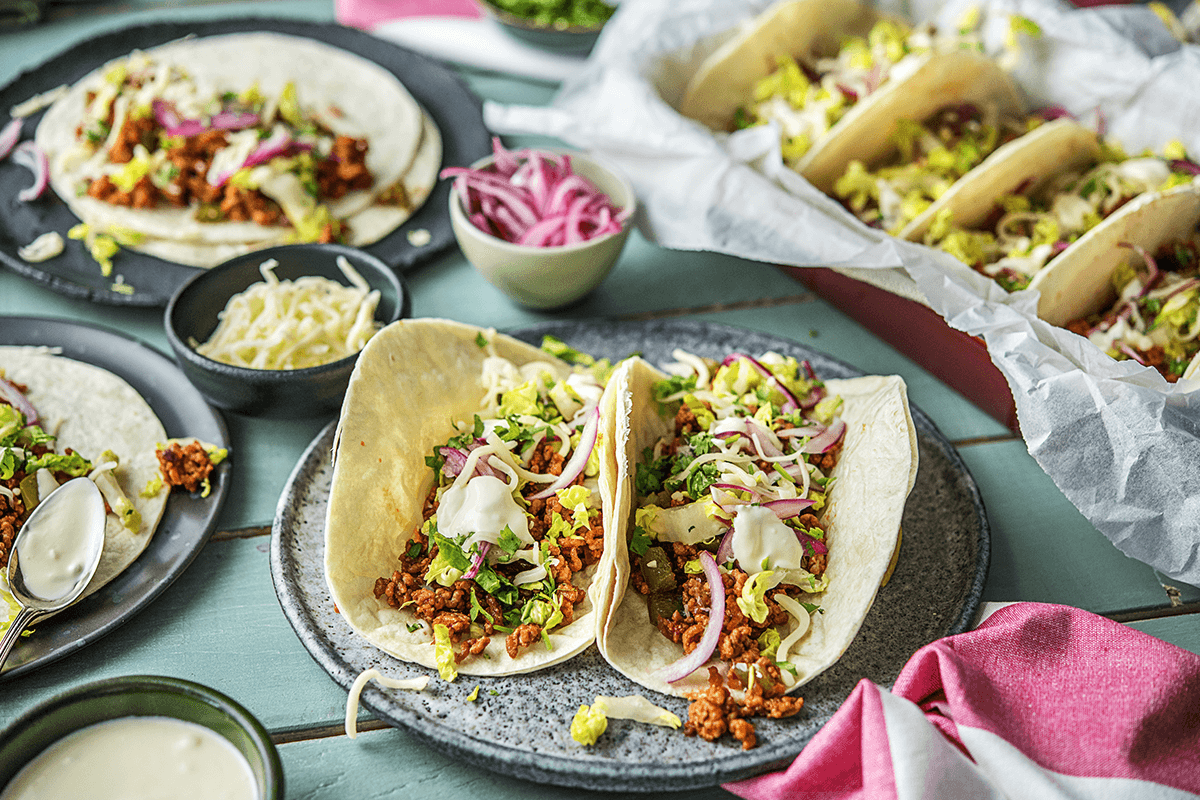
Impact
- 70% reduction in supplier costs (from $1,000 per supplier per year to $300)
- Achieved Safe Quality Food (SQF) certification at all U.S. facilities
- Enhanced document access and employee training adoption
- Streamlined supplier audits and corrective actions
Outcome
By implementing Intelex’s Supplier Management and Document Control applications, HelloFresh streamlined supplier audits, corrective actions, and quality control processes. This resulted in cost savings, improved compliance, and increased efficiency across global supply chain operations.
The Challenge for HelloFresh
As HelloFresh rapidly scaled to meet demand, the company faced growing pains: inconsistent supplier oversight, fragmented documentation systems, and a reliance on manual tools that couldn’t keep up with the pace of growth. With over 600 suppliers and a perishable product requiring precision, HelloFresh needed a solution that could centralize processes and build a sustainable, scalable foundation for quality and compliance.
The company had outgrown a costly supplier management tool that lacked internal transparency. Teams struggled with inefficient corrective action tracking and limited visibility across functions. With increasing pressure to meet SQF standards and manage an expanding supply chain, HelloFresh needed more than software—it needed a system it could shape around its evolving operations.
How Intelex Helped HelloFresh
Intelex provided HelloFresh with a customizable platform that empowered the company to align cross-functional teams, centralize documentation, and enhance supplier collaboration. Modules like Document Control and Inspection Management quickly became daily tools for production and quality teams. SOPs and training materials were housed in one accessible location, streamlining compliance and improving audit readiness—especially during the pursuit of SQF certification.
Inspection Management eabled real-time tracking of food safety audits, while Supplier Management allowed HelloFresh to cut supplier costs from $1,000 to $300 per year—resulting in significant annual savings. Direct supplier access improved documentation accuracy and responsiveness.
As HelloFresh expands its use of Intelex to include Training Management and Customer Complaints, the focus is on fostering deeper employee engagement. The goal: shift the mindset from viewing Intelex as a system to checking it like a core daily tool—an essential part of delivering high-quality meals safely, at scale.